Tesla Home Energy Products Should Be Installed in a Factory
First-Principles Design and Industrial Mass Manufacturing for a 10x Improvement
The eco-friendly 375 square-foot origami house that’s built in a factory, shipped, and unfolded
All for the low price of $50,000.
Boxabl has invented a construction system perfect for industrial mass manufacturing.
The Boxabl system uses unorthodox materials and a unique folding design. Everything is preinstalled at the factory, then the walls, ceiling and floor fold up for shipping via standard freight or even towing by a big pickup truck like an F-250 or Cybertruck. It unfolds on site in less than an hour, and because of the materials and mass assembly, it comes with a price of just $50k for 375 square feet (35 square meters). Boxabl’s ultimate plan is to allow units to stack and connect to build almost any type of residential or light-commercial buildings.
Tesla’s Solar Roof, Powerwall and future HVAC systems all could be installed on a Boxabl assembly line, which could help dramatically accelerate the advent of sustainable energy and housing by drastically improving scalability and cost.
Why would we want to do this?
Well, Tesla’s home energy products have unnecessary costs and inefficiencies for:
Design
Shipping
Installation
Permitting
They're done one at a time with human labor out in the field, often in custom retrofitted installations.
To make matters worse, traditional roofing and electrical work can be dangerous, exposing people to potential hazards from falls, ultraviolet radiation, extreme temperatures, storms, nail guns, poor ergonomics, repetitive motion stress, and energized electrical wires.
Rooftop solar power is more expensive than utility-scale farms due to soft costs
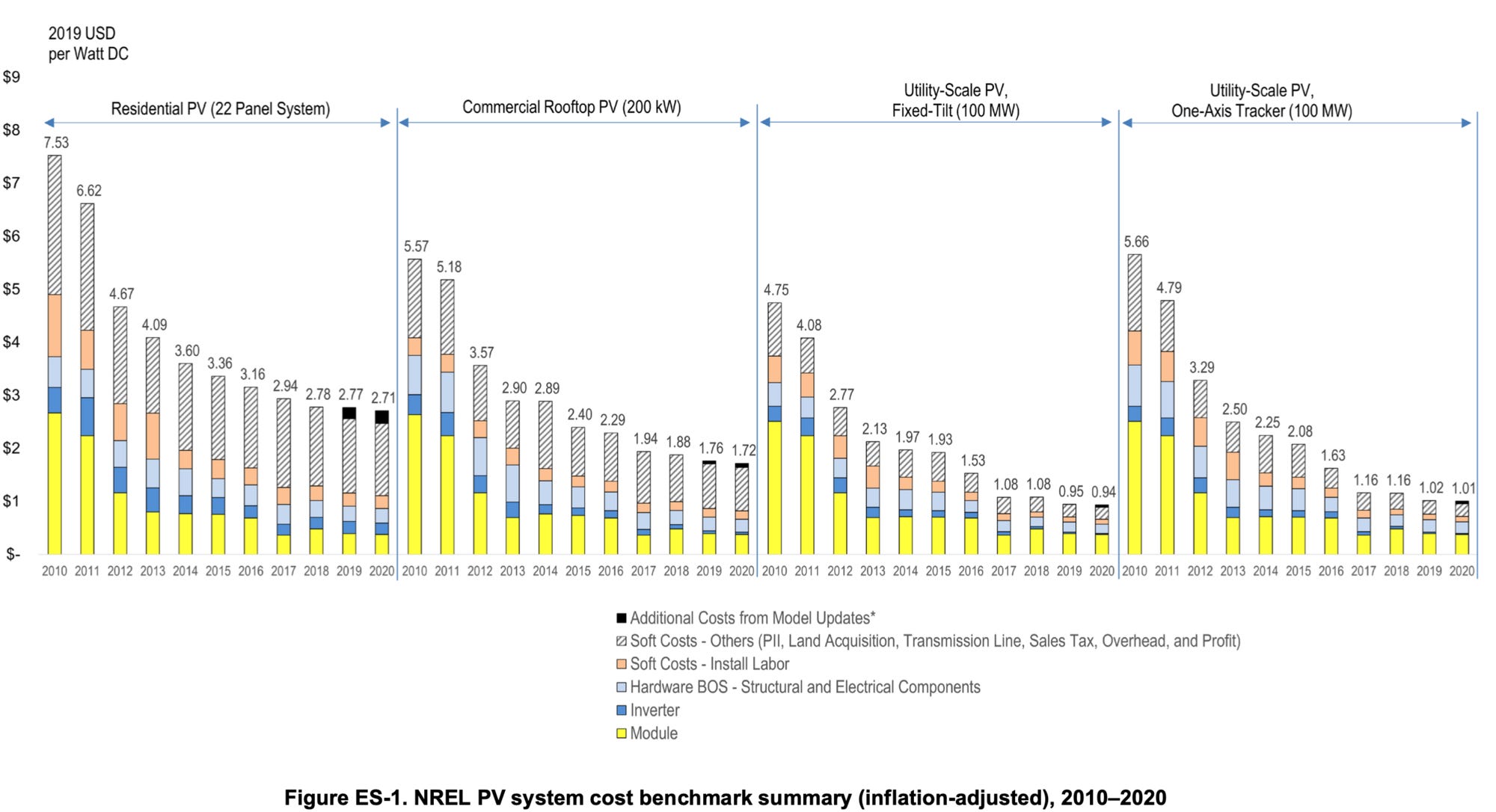
Those little yellow bars for the solar modules themselves are approximately identical regardless of the type of solar system installed, so that's clearly not the problem. Rooftop solar’s cost penalty compared to utility-scale solar is in soft costs, with some minor differences for inverters and the rest of the structural and electrical hardware. Small-scale on-site battery installations have similar cost problems compared to utility-scale batteries.
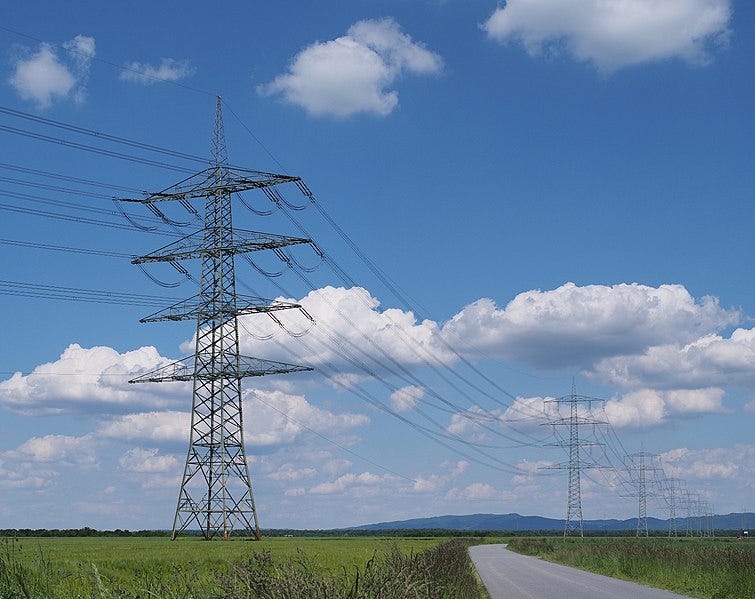
However, utility-scale solar/battery power plants have a downside as well; they are typically located far away from the load, often on the order of 5 to 500 kilometers of distance. This necessitates large-scale electrical grid transmission and distribution infrastructure that is:
Expensive; for instance, the average all-in costs of delivering electricity in the United States are around $30 per megawatt-hour (MWh) according to this 2018 study from University of Texas-Austin
Aging, with big, looming maintenance and equipment replacement investments on the horizon
Run by centralized monopolies that often don't behave in a prosocial manner and typically just seek maximum rents on their assets
Increasingly vulnerable to threats from climate change-related natural disasters, terrorism and cyberattacks, resulting in costly power outages
$30/MWh is a lot for transmission costs, considering that in many areas of the world utility-scale solar is already being sold for less than $30/MWh, such as the Al Dhafra project in Abu Dhabi selling solar-generated electricity for a record-setting $13.50/MWh.
So the trend is for solar photovoltaic electricity generation to get cheaper over time and it’s now starting to reach prices so low that transmission of the power from the solar farm to the load is the majority of the cost structure, and that fraction is increasing over time as transmission costs are rising while solar costs continue falling. At $10/MWh solar, which is likely to be achieved in the Middle East by approximately 2024 or 2025 if cost improvement trends continue, then transmission would be 75% of the overall cost structure if we use $30/MWh transmission cost as a rough guide.
We need to get the proximity benefits of collecting energy from photons striking the top of the building in which the energy is being used, while also deleting the traditional cost penalty of residential solar.
But how?
Most of those rooftop solar soft costs shown in the NREL data are for sales, overhead, installation labor, design, inspections, and permitting. Imagine if every Tesla Model Y order order began with a Tesla employee first driving out to meet with the customer and discuss their particular automotive needs, then coming up with a bespoke design for the customer, followed by handcrafted manufacturing and assembly in the customer's garage or driveway, and then government inspection and approval that needs to be fully completed before the customer can legally start driving their new Model Y. That would be totally absurd, right? But that's essentially the current model for Tesla Energy's residential solar, battery and charging products and would be the model if they were making HVAC systems already! Why are we doing it this way?
From a first-principles lean manufacturing standpoint, this is extremely inefficient and it’s not ideal from an ethical standpoint either because people are at risk of getting hurt or dying while at work. I roughly estimate that approximately 90% of the total activity involved is non-value-added waste that isn’t fundamentally required to arrange the atoms into the final configuration in the customer's desired point in spacetime for delivery. Therefore, this is a 10x disruption opportunity.
Key examples of non-value-added waste activity in current Tesla process from factory to final installation:
Scoping out site beforehand and meeting with owners and other customer acquisition tasks
Shipping hardware from factories to various sites
Crew driving to and from site
Moving hardware and tools from truck to building
Setting up ladders
Attaching fall hazard personal protective equipment
Climbing up and down ladders
Setting up work area and cleaning up when done
Walking around on the roof and in the house
Avoiding banging into doorsills when bringing stuff into house
Manually lifting solar roof tiles onto roof
Bending over to pick up roof tiles and turning to nail them into place
Manually installing nails, screws and other hardware
Measuring distances and marking lines with pencil
Carefully aligning tiles by hand
Plugging in wire connectors by hand
Getting separate permitting for each installation
Waiting around for approvals
Learning electrical setup of house
Fixing any quality errors due to manual assembly and roof imperfections
Working around weather disruptions
When it's listed like that, this process actually sounds comically ridiculous, doesn't it? A huge amount of the activity is actually just useless due to bad design. Tesla’s home/commercial energy and thermal product family should be installed on a proper industrial moving assembly line and robots should do most of the work, or ideally all of it.
Scaled up across the world, the better industrial model could save a staggering amount of wasted labor as well as copper, aluminum, steel, concrete, transformers, circuit breakers, and so on. The best inspection is no inspection. The best substation is no substation. The best high-voltage transmission line is no high-voltage transmission line. Delete and simplify and just make off-grid housing or local microgrids like Tesla did in Puerto Rico and American Samoa. The factory model with standardized, indoor, robotic mass production can almost totally annihilate much of the cost structure for rooftop solar, leaving a net total system cost that might actually end up being lower than utility-scale due to the superior installation efficiency, lack of land costs, and dual benefit of providing a roof in addition to electricity.
But how?
That where a Tesla-Boxabl partnership could come in
First, what is Boxabl?
Boxabl has, I think, the world's first and only commercially viable solution for mass manufacturing of housing. The Cybertruck of housing:
First-principles material selection
Design for manufacturing
Extreme durability and longevity
Can go anywhere
Stressed-skin structural exterior exoskeleton made of sturdy steel sheets
Apocalypse-resistant
So bold and radical of an idea that nobody is even attempting to copy it probably because they either don't comprehend the significance of what they're seeing or because they don't have the self-confidence to differ that much from conventional wisdom.
Guess who bought the first prototype Boxabl unit a couple years ago and has it in his backyard in Starbase, Texas?
Normally I don’t care about celebrity product endorsements, but this one is unpaid and I think Elon Musk is a special case with respect to endorsements of new technologies and I highly respect his opinion on this kind of stuff. This was a rumor Boxabl had been heavily hinting at since delivery because they were under an NDA, but the Tesla Technoking finally admitted to it two months ago on the Full Send podcast (warning: some swearing in this interview, may not be safe for work). Brief discussion of Boxabl at 41:45:
Host: What's with the Boxabl rumor?
Elon Musk: I do actually have a Boxabl, yeah. Some prototype Boxabl that's down in south Texas, yeah.
...Host: What do you think of the Boxabl?
Elon Musk: Yeah, it seems good...I don't actually stay in the Boxabl...the house that I actually bought costs less than the Boxabl. It cost like $45k or something—but I've done a lot with the place, you know ... I use the Boxabl as my guest house ... if a friend comes and stays or something, then they can stay in the Boxabl if they want.
I have spent hundreds of hours researching Boxabl and the prefab/manufacturing housing industry and if TSLA weren't so low right now I'd probably be contributing to Boxabl's Series A fundraising round, which is currently still open to Accredited Investors (link). In this post I won't get into detail about why I think Boxabl is so Excellent, but you can find all my notes and calculations in this spreadsheet:
https://docs.google.com/spreadsheets/d/14UjXW5WJC8c5yMtwLl28wDNO-YXKNuc0fP8-ujZc7y8/edit
Here's a really good introduction to Boxabl from Ellie in Space that was published in September:
Here is an interview containing more technical detail with Boxabl Cofounder and Director of Engineering Kyle Denman:
Boxabl can provide the substrate upon which Tesla’s energy ecosystem can be built.
Key advantages:
Moving assembly line
Standardized mass production and standardized verification of conformance to design and regulatory requirements
Numerous opportunities for end-to-end software automation
Rapid snap-fit robotic installation for roof tiles probably possible
Controlled indoor environment
No weather disruptions
24/7 operation possible without lighting or noise constraints
Consistent temperature
Even humidity can be controlled if needed
Minimum inventory
Optimal logistics using bulk freight and loading docks, or with an extreme integration approach, opportunity for setting up Tesla lines as feederlines outputting modules directly to point of installation in Boxabl line
Extreme quality (i.e. consistency)
Product is turnkey and totally ready for customer upon delivery to site after less than an hour of easy installation
Right now, Boxabl is leaving any special roofing up to 3rd-party contractors, but in the long run they plan to install solar at the factory as well. The only reason they're not already doing this is that they don't want to bite off more than they can chew, since they're facing a backlog of 150 thousand orders for their minimum viable product, the Casita, which is accumulating new orders far more quickly than Boxabl is currently able to produce units.
With extreme integration, it’s possible in theory to directly connect Tesla production lines for solar roof tiles, Powerwalls, HVAC systems and wall chargers to Boxabl production lines by using a feederline factory design, Even if this kind of combined factory doesn’t make sense practically, at a minimum there would be a big efficiency advantage of being able to ship tiles, Powerwalls, HVAC and chargers in full semi truckloads and unload them at lineside loading dock bays, like Boxabl is doing with the refrigerators and other appliances and materials. Logistics is much easier and cheaper with bulk freight, heavy-duty trucks, trains, and loading docks than a small crew driving a pickup truck or work van to multiple sites.
The Boxabl architecture seems to be the most eco-friendly construction design I have ever seen, and it's not even close unless we want to count primitive housing made by hand with organic materials, like traditional adobe or log construction. This meshes perfectly with Tesla's mission of driving human civilization towards sustainability, for which goal solving energy consumption and generation is one necessary but insufficient piece.
The Boxabl founders openly admire and support Elon Musk, drive Tesla cars, and are clearly copying the Musk company way with first-principles design engineering and focus on manufacturing and logistics and fun. Engineering runs the show and they appear to be rapidly iterating. One of the cofounders, Galiano, allegedly spends 16 hours per day working right now and spends a lot of nights sleeping in the prototype Boxabl unit next to the factory so he can get back to work sooner and spend less time commuting. I called Yanni, the investor relations focal at Boxabl and asked point-blank if Galiano is actually doing this and if it's really a sustainable workload, and the answer was that in fact Galiano is because it's his passion and we'll see how sustainable it is. Galiano's main job is recruiting capital and marketing, so that doesn't get too much harder with production scale.
If anyone at Tesla with influence reads my posts, I want say that I hope that Tesla will make a partnership like this. I think Boxabl has an excellent solution for sustainable housing, but they really need capital badly in order to make a bigger factory with robots and really invest in R&D to take the design closer to perfection. Boxabl could also benefit greatly from Tesla’s manufacturing expertise. They already got extensive help from Porsche Consulting, but as we all know, Tesla is on a whole other level with respect to manufacturing prowess. Alternatively, maybe someday Tesla could acquire Boxabl and help it scale. This would be quite similar to the 2016 acquisition of Solar City that got Tesla into the energy business in the first place in order to broaden the sustainability mission and capitalize on synergies between battery business, solar business and cross marketing opportunities. Tesla has already been partnering with developers like Brookfield to make subdivisions and wants to run a portfolio of distributed energy assets managed by Autobidder, but Brookfield is still building expensive stick-frame houses the old-fashioned way, not in a proper factory.
Moreover, for a strong initial market segment to pursue while scaling this idea, this Tesla-powered Boxabl design would have similar appeal as Cybertruck for the “prepper” crowd wanting independent off-grid home setup, and thus these products could easily be co-marketed.
Any Boxabl copycats that eventually enter the market could partner with Tesla too. The main point is that the best way to solve for minimum cost and highest quality and highest production volume to maximize rate of transition to sustainable energy and sustainable housing in general is to industrialize the operation and mass manufacture in a proper factory. First principles clearly point this direction and Tesla is a logical engineering company that always eventually does what physics first principles dictate as being optimal.
Addtionally, with Giga Shanghai and especially what was seen at Giga Texas, Tesla is finally moving closer to the vision of the ultimate factory that operates using the vertical dimension, being designed like a modern integrated circuit. Roof tiles could be fabricated on 2nd story maybe and then lowered down into place like how mating of Tesla body-in-white and skateboard is being done with the structural pack. If not, at least a factory will have cranes or other apparatus that can lift up solar roof tiles to the roof height where a robot could click them into place if Tesla can develop a 100% snap-fit design. No more ladders and manual pulley lifts.
Tesla also wants their HVAC system to be capable of distilling clean freshwater that could be connected directly to plumbing easily with the Boxabl design, again taking advantage of all the benefits of mass production in a factory.
This is how to make a production line to crank out a thousand solar roofs/powerwall/HVAC/charger installations per day.
But wait, there's more...
SpaceX is trying to create a self-sustaining civilization on Mars with a target population of one million people as soon as possible. They will need a lot of rapid habitat construction to do that.
But how?
Here are the special requirements I can think of:
Extreme affordability
Extreme manufacturing scalability
Fitting in the cargo bay of a starship with good volumetric efficiency (Starship has 30-foot or about 10-meter diameter)
Surviving launch stresses such as acceleration, vibration, and temperature
Easy deployment on Mars
Minimal installation time
Minimal labor, particularly specialized labor like plumbing and electrical
Minimal tools, particularly specialized tools
Concrete foundation not necessarily needed
Towable from launch pad to installation site by a Mars-edition Cybertruck or similar general-purpose utility vehicle
Extreme thermal insulation
Radiation shielding
Tightly sealed air envelope
Solar panels, batteries, vehicle charging and HVAC, all preinstalled on Earth
Pleasant to live, work and play in for people who will have to spend almost all their time indoors
Modular Lego-like design that's easy to stack and connect to additional units or remove and relocate from original site
Extreme durability over decades or preferably centuries in harsh conditions on Mars
As far as I can tell after having researched the industry and a wide variety of different house construction designs, Boxabl is the *only* company making anything with an architecture that could meet these requirements with some design changes for a Martian version. To make thing more interesting, in one short video on their website Boxabl vaguely hinted at potentially putting their units on Mars for Elon Musk, suggesting that they are thinking of doing this in the long run. I have no expertise in designing Martian habitats for creating an independent backup copy of the biosphere, but this looks like a promising architecture.